Cement is the only major industrial activity that gets Kashmir a degree of self-sufficiency. But a series of attempts at various levels have been underway to undermine the advantage, the latest being a cabinet order forcing government departments to purchase from crisis-ridden JK Cements Ltd, a Kashmir Life investigation.
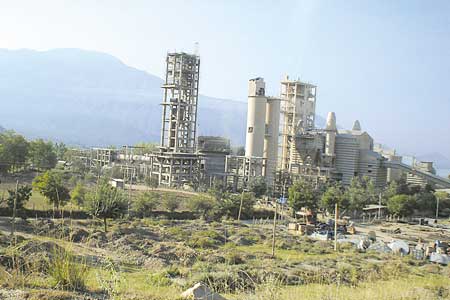
In the June 23, 2011 meeting of the state cabinet, one of the decisions that did not get the attention it deserves was about procurement of cement. The cabinet approved the proposal of the state industry ministry that the government departments should purchase their requirement of cement in the Kashmir valley from J&K Cements Ltd, a wholly owned state government company, on first preference.
The departments can procure cement from open market only when J&K Cements Ltd (JKCL) is unable to supply the requisite quantity and a non-availability certificate from the company is obtained by the purchasing government department.
Apparently, the proposal is just a reiteration of what was already in place. The issue was taken to the cabinet for the first time to ensure that there are no violations. This order leaves out Jammu where departments purchase from big players outside the state.
Over the years, Kashmir has recorded substantial investment in the cement sector. Estimated at around Rs 700 crores, the investment was motivated by the availability of raw material (mostly limestone) and a local market. There are seven cement manufacturing facilities in Kashmir, three are major brands – Khyber, TCI Max and Saifco – that have high-end plants and dominate the market.
“Our cumulative production is 4000 tons a day which means 80,000 bags,” a major manufacturer said, adding, “Some small unit holders are investing to add up capacities.”
For years the private manufacturers were selling in the open market as the over-protection by the government helped JKCL to retain its monopoly over the government purchases. In 2010, Khyber fought a protracted legal battle on the basis of quality and the systems involved in the production and won a judicial intervention that made them eligible for supplying to government departments. The battle did not only offer a legal entry into a comparatively lucrative market but also helped the State Procurement Department Store (SPD) revive its Kashmir operations. The department had a skeletal presence in Kashmir as most of its operations were carried out from Jammu.
Khyber, the market leader is supplying – albeit a limited quantity – to the SPD for the last two years. Any change in the systems involving purchases could force a status quo ante and force an unfair practice in the market. This disturbed the JKCL because it could mark the end of monopoly. The cabinet decision is apparently aimed at protecting the unfair practice.
But JKCL has problems beyond the marketing of its manufacture. In all the commercial activities of the state government, at one point of time JKCL was one of the best performing units. The onset of militancy saw the workforce losing work hours and as lack of uninterrupted power supply added to the mess. It survived with massive losses amid severe labour unrest up to 1997.
In March 1999 it had eroded its paid up capital of Rs 15 crores to the tune of 62 percent by incurring a loss of Rs 9.30 crores. Against a total of 17,520 working hours available to its man-power for a year, it lost 4313 hours in 1994-95 in strikes and holidays, and 6,374 in the subsequent year.
After October 1996 the trend reversed. In 1999-2000 it lost just 3,133 hours. The idle hour percentage was 43 percent in 1994-95 and it fell to mere three percent in 1999-2000. By 2001-02 JKCL registered an all-time record turnover of Rs 40 crores, cleared almost all its cumulative losses and outstanding loans amounting to Rs 5.50 crores.
By the end of the National Conference government in 2002, the JKCL had paid Rs 7.25 crores as Sales Tax and registered over two crore rupees of profit after paying wages to its 680 employees. It was then that the government decided the JKCL needs upgradation and expansion. A debt free company, it paid Rs 45 lakh dividend to the state for the first time in 2001-02 since its inception in 1981.
The JKCL survived on its main 550-tons per day (TPD) facility at Khrew. Its decision to upgrade and expand in a single go disturbed its growth script, something the management disputes. By 2003, JKCL got the cabinet approval for setting up of an additional 600-tpd plant at Khrew at a cost of Rs 87.50 crores.
When JKCL finally invited the then chief minister Ghulam Nabi Azad to lay the foundation stone for the project to be implemented by the Bangalore based Promac within 26 months on October 27, 2006, the time-overruns had added to the costs.
At the time of the agreement the project cost Rs 94.52 crores – Rs 32.27 crores equity by the government, Rs 6 crore contributed by JKCL as balance Rs 62.25 crores was the debt raised from J&K Bank. Debt servicing schedule – almost Rs 12 crores a year – started after 26 months. It did not stick to the deadlines but the plant did come up. By January 2009 the new machinery was in clinker-production. By December 2010, it produced 16,776 mts of clinker. But that never meant it was officially commissioned.
“The single klin plant is manufacturing but officially it is yet to be taken-over by us,” Mushtaq Ahmad Malik, a chief engineer rank officer who took as Managing Director in April 2011 told Kashmir Life. “It (takeover) is likely to take place early 2012.”
“It obviously is in tailspin,” said a senior officer who was formerly associated with the project. Insiders tell a larger story with all the routine elements that historically remained associated with the undoing of the project. “We have the sixth MD sitting in the chair since the project started and every boss takes six months to understand the issues and well before he starts asserting on things he is out. There is no continuity.”
The project, insiders say, is in place but it is yet to yield what is expected to. “It should fetch us 600 tons of cement a day at a per ton input cost of 19 tons of coal and 20 units of electricity,” said an officer. “We are willing to takeover the project if it runs on half the capacity in the first year but it has an efficiency of only 30 percent which is unacceptable.” Executives say Promac is working overtime to fix the plant so that it testifies to the performance test guarantees.
Promac had cited various factors responsible for low production that included low voltage electricity supply during winters. This sent JKCL spend Rs 40 lakhs for managing generators from Delhi on rentals but that also was of little help. Sources at the plant told KL that it consumes 32 tons of coal per ton of cement besides a lot of other energy, something the management refutes. “Even if it gets us the tonnage that we require, it has to yield it within the permitted limits of fuel consumption,” said a senior official with technical knowhow. “Otherwise it is economically not viable.”
The JKCL had hired M/S Ercom as consultants for the project. They got nearly one crore rupees as fees but were allegedly “kept away from day one”. Now they are unwilling to respond to the JKCL requests.
Insiders allege that JKCL released 10 percent of contract amount that was supposed to be kept in company vaults till the project is handed over, apparently under “pressure of vested interests”. But MD Malik says “it is five percent under the agreement which is with us and we have additional Rs 1.5 crores still with us.”
“It (JKCL) is sinking so fast that well before we could think of freezing the fall it will be over,” a senior officer who retired from the company said. “It is a mess of a management because you have 850 employees but there is no balance. You need engineers, they are quite a few, and you require a few officials and you have an army.” The company has skipped employing for the technical positions that has created a scenario where chemical engineers are working under novices, alleged some insiders.
The new project is yielding some clinker, the debt rescheduling is on and the improvements worth Rs 5.30 crores of the functional old plant are gradually taking place. It is a sort of crisis that the management is not admitting. Its cement production fell from 163640 tons in 2009-10 to 137041 in 2010-11. Many think the profits are an outcome of hiking the selling price by Rs 39 a bag.
“Production decreased simply because of the turmoil in 2010,” said Malik. “This year situation is better and we produced 43030 tons in first quarter and we will achieve the 180 thousand tons in the current fiscal.”
It is in this crisis the JKCL started setting up a grinding unit at Samba (Kathua). Supposed to be at the tail end of the priorities, insiders said, industry minister Surjit Singh Slathia is keen that it should happen on priority because it falls in his constituency. “The idea is to get it ready before the new elections and it is supposed to consume clinker that comes from Himachal,” an official claimed.
The government has already purchased 20 kanals of land from SIDCO for installing a 300-tpd grinding unit that would cost Rs 12.58 crores (now around Rs 20 crores). For political reasons it is being put in fast forward mode and that would add to the surging liabilities of the company. The company has exhausted all its resources to manage the debts. “The issue is where from the JKCL will lift the money to manage its surging requirements,” asks a middle rung officer. There are problems, says the MD, but there are solutions as well. He, however, chooses to keep his solutions to his chest.
The ridiculous part in the entire story is that JKCL purchases clinker from outside that costs a fortune. Clinker is grinded to create cement. For a long time, JKCL imports clicker from three major cement manufacturers – Shree Cements Rajasthan, Ambuja and JK Laximi – that comes in rail-racks to Jammu wherefrom it is transported to Khrew for grinding. “It is very costly. Our own clicker costs us Rs 3000 a ton but the clinker we get from outside costs upward of Rs 6500,” said an insider. This is because the two plants of JKCL are unable to manufacture the clinker that the old plant requires.
The option available with the JKCL was to procure the clinker locally. “We are in a position to offer them clinker at much lower rates which would eventually help them reduce costs,” one senior executive of the major cement manufacture told Kashmir Life. In fact, a retired executive of the JKCL revealed that he had submitted a proposal suggesting clinker be sourced locally because it makes an economic sense. “The (then) MD told me that I had taken bribe from Khyber so I closed my mouth never to open it again,” the erstwhile officer who wished anonymity said.
MD Malik says they purchased only 11000 tons of clinker last year. “We can not procure it locally because of quality issues,” he says referring to a test carried out by a third party. Interestingly, the plants of all the major manufacturers in Kashmir are of same standards and all use the same technology but “qualities differ”. Insiders, however, say JKCL thinks it is “suicidal” and “a marketing defeat” because sourcing raw material locally “can be played against our brand.” MD says JKCL never compromises on quality that is why even the Jhelum, the brand that it markets, is used by Airport Authority of India and most of the major power projects. But a serving officer admitted: “Earlier it (purchasing clinker) was justified but now with a new plant it is not.”
It is in this atmosphere the cabinet wants to protect the market for the JKCL that produces slightly less than 10,000 bags of cement a day. The cumulative production in the private sector in Kashmir is 80,000 bags a day. JKCL sells at Rs 330 per bag in Srinagar to the government and Khyber sells Rs 248 to the SPD at Jammu. “The SPD at Jammu purchases well over 35 lakh bags a year and in Kashmir it is less than a million bags,” informed a private manufacturer. “Why is the government penalizing its departments because it is unable to manage JKCL? It is tax payer’s money and the best cement is available at around Rs 100 less than what the government is keen to purchase at.”
That is not the only problem. The Power Development Department is planning to get the cement manufacturing activity into the power sensitive category. The plans are to increase the tariff by around 153 percent. This will add to the in-put costs and reduce the differentials between the ‘imported’ and the local cement. Right now locals sell cheaper as compared to the imported brands.
Off late, cement consumption in J&K is soaring. Apart from local manufacture, J&K consumed 948000 tons in 2004-05 that was mostly supplied by the major outside producers. Consumption of non local cement continued to surge to 1014000 tons in 2005-06, 1240000 tons in 2006-07, and 1258000 tons in 2007-08. Once the local manufacturers started competing, it witnessed a fall.
In 2008-09 the supplies from outside registered a 14 percent fall to 1078000 tons. It nosedived further to 368110 in 2009-10 and for the last fiscal ending March 2011, outside companies supplied only 311293 tons. As the cement consumption across the state is hovering well over 15 lakh tons a year, it is the local manufacturer filling the gap. And it is this trend that policy makers want to arrest so that outside manufacturers revive their stakes in J&K market.
Private players see a visible discrimination in protecting the Kashmir market for the JKCL and leaving Jammu open to suppliers from outside. “If the government is protecting Kashmir, why do they not give the Jammu region to private sector of the state,” asked a senior executive of a cement company. “The decision seems highly discriminatory and blatant use of authority that lacks logic.”
MD Speak
Mushtaq Ahmad Malik took over JKCL’s top slot in April. He says the marked difference that distinguishes the PSU from the private sector is that JKCL staffers get sixth pay commission packages and the private sector works on minimum wages. The costs per bag, he said would soon be reduced as the new plant becomes fully operational. He says the delay in the implementation of the new unit is rooted in the disturbed situation in last three consecutive summers. The company that implements the project on turnkey basis, he said, is being tackled strictly as per the agreement. He said there are problems in JKCL as there could be in any other organization. “But we have the solutions,” he said, insisting, reports about sinking of JKCL are far fetched. He said the Samba operations would be pursued because there are commitments to the Jammu market. He said they have plans in place as far as funding of the project is concerned.